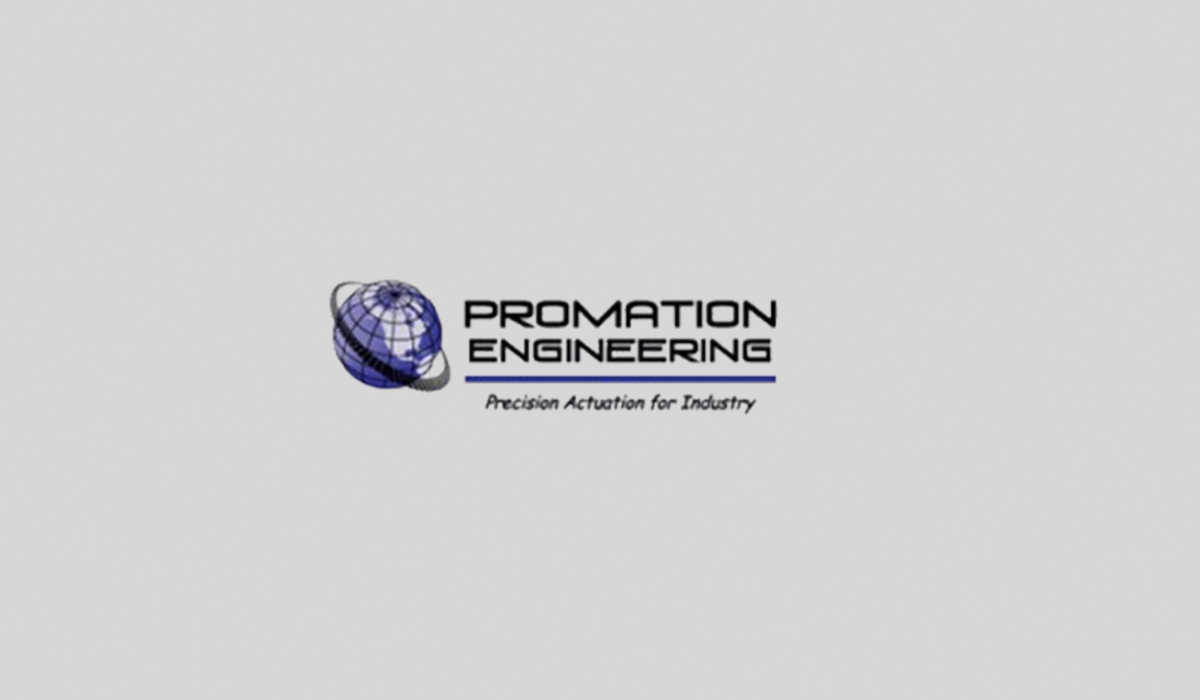
Notes from a hotel room: The difference between electric and pneumatic valve actuators
Notes from a hotel room while I am traveling the west, by Bill Knecht
I often go to facilities that are old and on their last legs and also get to be in on the beginning of a new facility or new technology and everything in between. I like to think about how things work and how to make them better for customers. So, in this age of instant communication I want to share my thoughts.
First, happy New Year!
Second, let’s talk about the difference between electric and pneumatic valve actuators. Pneumatic actuators can take many forms. They can be Rack & Pinion, Scotch Yoke, Vane, Diaphragm and even linear piston style. There are direct acting and spring return actuators. They can be set up in different fail modes. Air supply can vary but 80 PSI is a good norm. They are mostly 1/4 turn although there are a few variations but for this discussion the basics are good. Electric actuators can be 1/4 turn or multi-turn. They can be linear in motion, too. Voltages can be from 12VDC to 480 VAC or more in rare applications. There are Spring Return actuators and a Battery Backup system for fail safe applications. For this discussion, we’ll focus on the 1/4 turn.
Recently, the US department of Energy has called compressed air the 4th utility (electric power, natural gas, water, and compressed air). We will discuss the differences in the costs of air versus electric actuators. So compressed air is at the front of this discussion.
Let’s think like a design engineer: let’s say you have a facility you are designing and there are 100 valves that need to be actuated. The majority are on/off actuators, but there are a good number of modulating valves. In utilizing pneumatic actuated valves you need large compressors, you need air storage tanks, and a labyrinth of instrument air lines and associated drains and heat tracing of some kind. You also need to run a signal wire in addition to the control system. But it can be assumed that with a few minor differences, the control system for either pneumatic or electric is pretty much the same.
Electric actuators need the power delivered and for modulation, signal cables. Power can vary, and cables should not be run in cable trays with signal cables.
On the surface, the cost of a new compressor and air holding tank are a large up-front expense, the actual power needed to run the compressor essentially 24/7 and over time, more expensive. There will need to be a back-up generator with associated plumbing and wiring in case of power failure.
All the above reasons and more are why the Department of Energy has compressed air listed as the 4th utility. Next time we’ll discuss relative costs.
Come back often and we can learn together.